Oil and gas companies are using unmanned aircraft system (UAS) technology to improve safety and efficiency in a growing range of applications, from infrastructure and maintenance inspection to security, emergency response and environmental and regulatory compliance. Today’s UAS programs are supported by payloads including high-definition video equipment, high-resolution still cameras, thermal imaging cameras and emission sensors – and there are many ways, operationally and financially, to incorporate them into business processes. Numerous oil companies have demonstrated how UAS programs can improve safety while augmenting existing operations, and have also shown the value of supporting these programs with a comprehensive range of processes, procedures and management systems.
Examples of Successful Programs
One of the most popular applications for UAS programs includes visual inspections of remote assets such as oil rigs. In one example, a major oil company set up a UAS program to identify the presence or absence of rig components or subcomponents – as well as any gross damage or deformation, including visible cracks, the extent of coating breakdown and variations from structural drawings. The unmanned, eight-pile production and compressor platform included a boat landing connected by a bridge, and featured two decks and elevation depths ranging from -97 feet to 10 feet (Figure 1). Many of the areas of interest were in hard-to-reach locations, as the image shows.
Clearly, manual inspection of these rig elements would be both difficult and dangerous if it required sending someone down a ladder or out onto scaffolding. With a UAS program, people are removed from these dangerous situations. Additionally, inspections can be performed while the asset is live, thus reducing the length of costly shutdowns. A study of UAS use at one leading international exploration and production (E&P) company showed that these programs enable inspections to be completed 20 times more quickly than traditional rope-access techniques, which can take an average of eight weeks to complete when using human inspection teams. The direct costs of UAS programs are half those of human inspections – and UAS programs also eliminate other indirect costs associated with offshore bed space, standby boats and the transport of personnel to and from the rig by air or sea. The costs of helicopters, alone, can average as much as $2,500 an hour and up to $60,000 per flight.
When UAVs are used for all initial visual and thermal inspections, personnel are only deployed for contact inspection and other advanced investigations, if required. This can sharply reduce the risk of death and injury in a workplace environment that, according to the Occupational Safety and Health Administration (OSHA), has a fatality rate seven times greater than that for professionals in other sectors. One rig operator that implemented a UAS program reported a reduction in injuries of greater than 10 percent as compared to the same period a year earlier when it used human inspections. The other benefit of removing humans from these inspections is that it is no longer necessary to shut down rig operations, which can cost an operator millions of dollars in lost production. Assuming a typical five-day shutdown during a traditional inspection, the operator might possibly lose 100,000 barrels in lost production at a cost of $40 to $50 per barrel.
In a typical rig survey example, a UAS could capture visual images of key elements including cellar underdecks, emergency shutdown valve (ESDV) platforms, conductors and guides, caissons and jacket legs. Coverage of a cellar underdeck would be enhanced by having the UAS aerially inspect it from several different angles, taking both close-up and standoff photos. An interim inspection report is generally provided midway through a project, highlighting immediate issues and general conditions, and a final report is submitted at the project’s completion. A typical inspection report encompasses all key elements across multiple elevation depths. In the example of an unmanned, eight-pile production and compressor platform, this would include performing topside, hull and structural critical inspection point (SCIP) surveys. A UAS would be used to take topside photos of the structure, along with video footage throughout the inspection. The UAS would also be used to image the structural and coating condition on the hull exterior and associated components, along with the coating condition and surface corrosion on all columns and other SCIPs. Figure 2 shows the video log of a typical report.
The images in Figure 3 are among 1,900 visual images that were captured during a survey of a typical rig’s components and subcomponents. It shows a riser umbilical caisson platform to which access had been restricted because of storm damage. The images in Figure 3 show an 80 percent coating breakdown on the deck support leg, with surface rusting shown in the inset image.
The UAS survey identified numerous other issues, ranging from missing gratings and handrails to areas of moderate to heavy corrosion on jacket legs, horizontal bracing, conductors, and the welded connections in the areas between jacket legs and the underdeck and near discharge pipes. In the cellar underdeck steelwork, the survey showed that the primary member between two grid points displayed complete coating breakdown and surface corrosion, with exposed reinforcing mesh shown in the inset. This area would have been extremely difficult for a person to survey (Figure 4).
One of the most difficult locations for human surveyors to observe is the flare and its supporting structure. This location is relatively easy for a UAS to survey, as shown in Figure 5. In this example, liquid staining has occurred, providing evidence of process fluid that may have been discharged during a blowdown or process interruption.
To view Figures please click on the link below
Get some quotes for a drone operator
✔ 100% free service✔ Featured in the SMH, The Age & WA Today
✔ 1,800+ online recommendations
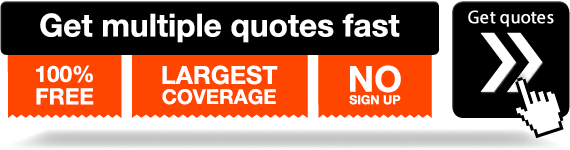