Measure, a provider of drone services to enterprise customers, has added turnkey wind-farm inspection capabilities to its portfolio of aerial data collection solutions. Wind-farm operators can now outsource preventive maintenance inspections to Measure’s drone pilots and data analysts for fast, accurate, safe, and timely problem identification. The service is designed to help avert critical turbine failures and efficiency losses while reducing repair downtime and its associated revenue impact.
“Many wind-farm owners don’t inspect their turbines on a preventive maintenance basis, and those that do use ground crews with conventional cameras and zoom lenses. Under both conditions, there is a risk of failing to detect turbine damage or structural defects on blades that can worsen over time and lead to a catastrophic failure,” said Harjeet Johal, Measure VP of Energy Infrastructure and a 10-year veteran of the renewable energy industry with a PhD in electrical engineering.
“Our drone-based inspections provide multiple advantages that can help wind farm operators operate at peak capacity,” Johal added.
Measure’s package spans all inspection and reporting functions, including state-of-the-art drone equipment, safe and insured flights by experienced drone pilots, efficient data processing that pinpoints blade damage and severity, and damage reports and analytics available through a secure online portal.
Benefits of Measure’s drone-based blade and tower inspections include:
- About 75% faster inspections than other methods, averaging 30 minutes or less per turbine compared to as much as two hours for manned inspections. This reduces excessive time commitments and allows large wind farms to be inspected more frequently. It also reduces labor costs for inspection and frees employees for other tasks.
- Decreased injury risk in the field, with no threat of falls to inspectors climbing turbine structures or blades.
- Better defect and damage detection because drones get closer to turbine blades than ground cameras, capturing clearer images. Undetected defects on the blades can result in continuous efficiency losses as high as 6% and associated revenue loss of up to $10,000 annually per turbine.
- Maximized turbine availability and revenue generation through early problem detection that helps prevent critical failures and associated downtime for repairs.
- Actionable data, including classified damage reports and historical portfolio analysis documenting turbine defects, failure rates and efficiency losses over time. Damage reports can be customized to display only the information needed by blade repair technicians with a few clicks.
Get some quotes for a drone operator
✔ 100% free service✔ Featured in the SMH, The Age & WA Today
✔ 1,800+ online recommendations
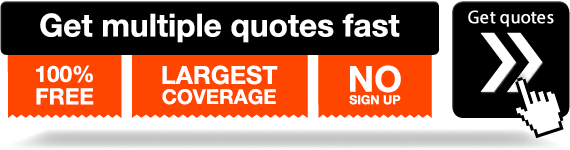